
Utility lighting for a storage container.
The first project that I completed with my new business was a rather unique take on utility lighting for the inside of a storage container.
The customer requested interior lights that were motion activated, and most of the rest was left up to me.
One of the more interesting aspects of this build was how to provide power for the lighting. The storage container had no power connections whatsoever, so I decided to make some.
In essence, I created a small solar power system that would supply electricity to the lights at night via a small deep-cycle battery.
I then took the entire system and incorporated it into a small metal box which could be mounted inside the storage container.


The partially assembled power box, complete with motion sensor, fuse holder, and solar charge controller.
Here you can see how the components will go together once the system is installed.
Overall, the idea was to create a reliable system which I could install in a short amount of time once on site. As such, I built the majority of the system off-site, and did my best to optimize the system for a quick installation.
Because there was such a large emphasis on making the system easy to install, the longest part of this project was actually research, design, and construction of the system--taking around 10 hours of work to complete.
Even basic items such as the solar panel mounts were revised several times prior to installing the finished product.
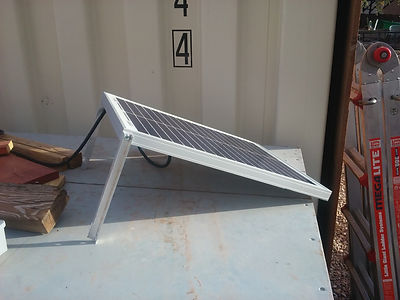
I used a single, 20-watt solar panel to supply power to the system.
Aluminum channel was bolted to the top end of the solar panel to provide an easy way to mount it to the container.
The install went very smoothly. In fact, the only major issue that I had was drilling through a roof beam on the storage container to mount the solar panel. I destroyed several drill bits before I managed to get the panel mounted properly.
In addition, various features inside the storage container made it extremely easy to mount the lights and the wiring.
All in all, the final install only took around 4 hours to complete. This was quite the pleasant surprise, as I expected to have much more trouble given the lack of mounting hardware in the storage container.
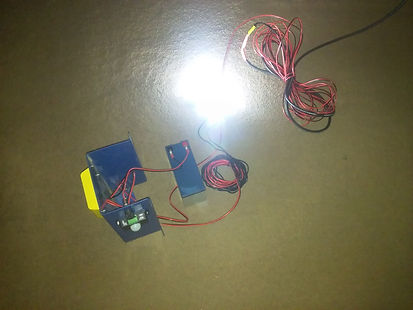
Once the system was completely assembled, I performed a full running test to make sure everything was in order.
Here you can see the system running for the first time, complete with insanely bright LED lights.

The power box in its permanent location, bolted to the inside of the storage container.
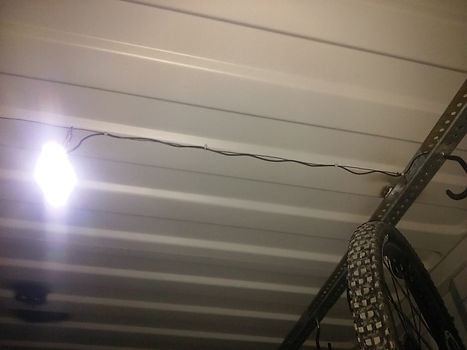
Metal channels inside the container provided a very nice place to attach wiring, as well as a good way to hang the lights.
The lights were suspended by cables strung between the metal channels.
Although I would call the project a success because the customer was happy and my design worked as it should, the project was not without its issues.
The most important obstacle that I faced was budgeting. Since every project is custom built from the ground up, predicting extraneous costs (especially hardware) was quite difficult at times. Since this was one of the earliest projects that I undertook, budgeting proved to be one of the most difficult and educational aspects of the entire project.
As with anything else, this project had quite the learning curve, but all in all, it still went very well.

The finished product, blindingly bright and robust enough to last for years to come.
Custom DC lighting for a camp trailer
This is the largest single project that I have attempted to date in terms of labor.
The customer requested a complete lighting overhaul of a small camp trailer. All of the interior lights were to be upgraded to LED, and several new lighting systems were to be installed.
​
The first lighting system to be installed was purely for decoration.
By request of the customer, the lights were to be color changing, and fairly well concealed, as to not look like "Christmas lights."
I focused on creating indirect lighting, keeping all of the interior lights hidden behind various features inside the trailer. This was a very entertaining challenge, because I got to put a more artistic emphasis on the lighting design overall.
Finally, I put a small run of lighting outside the door to light the doorway at night.
​
Next was a lighting system for the kitchen sink and oven hood. For these lights, the customer requested that they be bright, but most everything else was left at my discretion.
Installing these lights was very straightforward, and the result was very clean. I was able to use the same parts that I had used for the decorative lighting with the color changing functionality removed.
While not necessarily as fun to build as the decorative lighting, the end result was effective and the customer was quite pleased.
The last part of this project was converting the incandescent DC light fixtures to use LED lights.
I took a rather odd approach when converting the fixtures to LED. Instead of using ready-made equipment, I built my own LED modules. I mainly did this because I could not find LED replacement bulbs of the correct type that were in the customer's price range.
By making the modules myself, I was able to deliver a finished product to the customer that was both brighter and cheaper than anything I could find off the shelf.
Overall, this project was a lot of fun, and the customer loved the result.
Since most of the lights that I used run on 12v DC, it was very easy to wire the individual systems into the trailer. In addition, several features inside the trailer made it easy to hide lighting and wiring without too much headache.
That said, this was without a doubt the longest project that I have ever undertaken. Almost the entirety of this project was completed on site, with maybe 2 hours worked off-site ordering parts and building LED modules. All in all, the install took around 14 hours to complete. It was a very long time to spend inside a trailer with a soldering iron, but the end result made it all worth it.
​
Amazingly enough, I didn't run into many issues with the hardware when performing the install, but I did underestimate the amount of time that I thought it would take to complete the install. As a result, I had to reduce my hourly rate slightly in order to stay within the original quote for the customer. That said, I would consider this project a success overall, as I still made an acceptable profit, and the customer was quite pleased with the result.

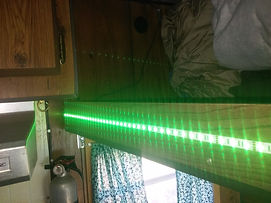
The first part of the decorative lighting, run on the edge of a drop-down cabinet. When folded up, the LEDs are hidden and the light reflects off of the ceiling, creating a soft glowing effect.
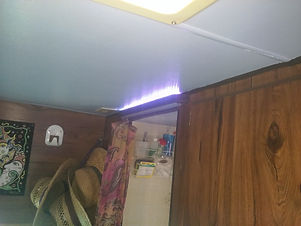
More indirect lighting, hidden over a small piece of door trim in front of the bathroom.
Here you can see how the light reflects off of the ceiling, creating a far less harsh form of light.

Rubberized ceiling trim made it very easy to conceal the wiring for the interior lights.
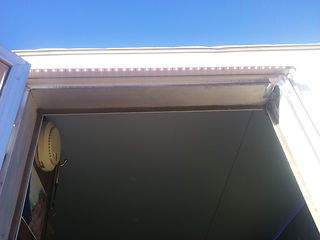
The only exterior lighting, installed right over the door to light the doorway. This also creates some very interesting effects at night, as these lights change color with the interior lights.
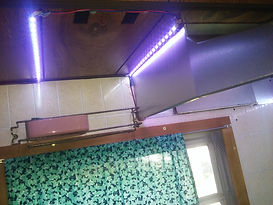

Utility lights for the kitchen were fairly straightforward and extremely bright. In addition, the lights inside the oven hood are mostly hidden when viewed from standing, making the brightness far more tolerable.
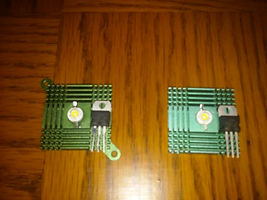
LED light modules for the DC light fixtures. These units were built from scratch and designed to be a permanent replacement for the old incandescent light bulbs. Each unit consumes less than half the power of the original lights, while producing over twice the brightness.

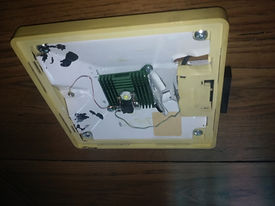
The LED light modules, permanently mounted in the DC lighting fixtures. These units are far brighter than stock and should easily last the life of the trailer.
Custom mobile power system with utility lighting
As a result of the first projects with my business going so well, I decided to start taking on more difficult projects as time went forward. This project was quite difficult, involving the design and installation of a complete power system as well as re-wiring of a utility trailer.
The customer wanted utility lighting for a trailer that was to be used as the center for a mobile catering service. As such, this trailer needed to be brightly lit for extended periods of time, and auxiliary power would most likely prove quite useful. As a matter of fact, the only two requirements were bright lighting that could run for a long time, and an auxiliary power jack. This gave me a lot of freedom when designing the system.
After some research, I settled on a rechargeable DC power system that had the ability to charge with either solar power or the truck that would be towing the trailer. Using a system that could be charged via solar allowed me to downsize the main battery and much of the power equipment, thus reducing cost to the customer with the added benefit of adding versatility to the system.
When it came time to build the system, there were several obstacles that needed to be overcome. Errors in wiring required rewiring of the main power unit multiple times, and running changes in the design to meet the customer's needs consumed a great deal of time. That said, most of the difficulties were in the initial design of the system. In fact, the initial design was the longest single portion of the project. From start to finish, the initial design (including research) took just shy of 8 hours, with the final installation only requiring 5 hours to complete.
Overall, this was a very fun project. Not only was this project interesting, it was very challenging, and the result was a success. The customer was also quite pleased with the finished product. After having such success, I feel much more confident taking on difficult projects and look forward to challenging myself in the future.
​
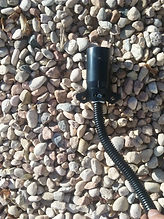
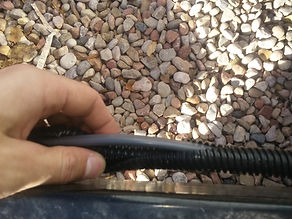
The first part of this project required replacing the main trailer plug, and adding a charge cable to the main wiring loom for the trailer. This allows the new power system to charge off of the truck while the trailer is being towed to its destination.
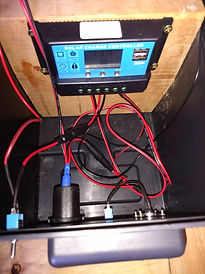
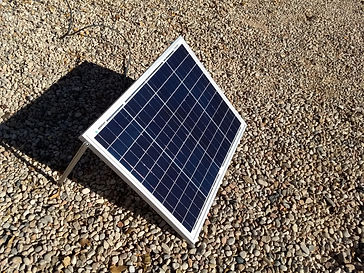
The main power system consisted of a small deep-cycle battery, and the solar panel shown above. The main power equipment was mounted inside a battery box along with the battery itself. This allowed the entire power system to be contained inside a single unit, with the exception of the solar panel, of course.
The solar panel is set up as a modular unit. once the trailer is on-site, the solar panel can be placed on the ground outside and a 20ft power cord connects the panel to the main power unit. This panel can supply enough energy to charge the main battery and run the interior lighting at the same time.
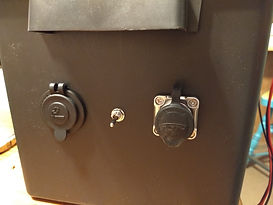

The main power system is contained in a simple trailer battery box. This battery box includes connections for both the external solar panel and 12V auxiliary power. The internal battery alone can run the lighting for 12-18 hours, and the system can run indefinitely with the solar cell connected. A main power switch controls the lights and the auxiliary power jack.
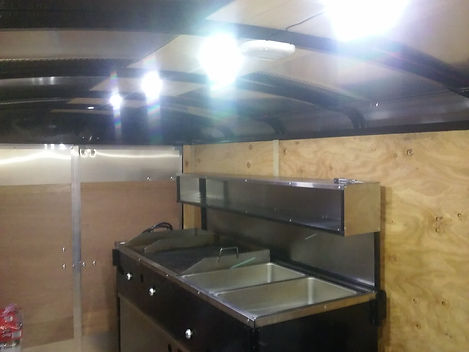
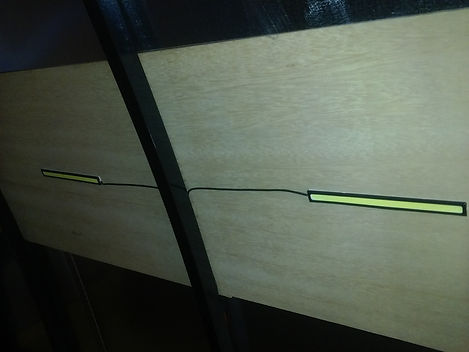
The main lighting consisted of four, 6W LED modules attached to the center of the ceiling. These modules were originally designed for use as automotive fog lights. As such, these units are resistant to high temperatures, and high levels of moisture. In addition, these units are insanely bright, creating good visibility with virtually no dark spots. An interesting result of having multiple lights in a confined space is that there are virtually no shadows when the lights are on. Finally, support beams that spanned the ceiling made it easy to attach the wires, making the finished install look quite clean.
Completely overbuilt "yard art".
This was a major change from the last project in many ways. This was the first completely stand-alone system that I had designed. This means that the system was to operate without any user input for years one end. In addition, this was the first project that was intended to operate exclusively outdoors.
These unique requirements presented their own unique set of challenges. I began by determining the correct type of LED lighting for the task at hand. Service life and resistance to the elements were of the utmost importance. Next, a battery system had to be specified for the lighting to provide complete dusk-dawn operation. The system then required a solar panel capable of charging the batteries within a given time-frame for the location. The final obstacle was packaging, as the entire system would be exposed to severe weather and temperatures in its final location.
This project ended up requiring a complete environmental study of the installation location to determine usable daylight hours for charging, expected operational hours for the lighting, and moisture and temperature resistance for the entire system.
The end result was a system that can reach full charge in around 8 hours, with enough capacity to run the lights at full brightness for around 20 hours on a full charge. The color and/or pattern of the led lighting can be programmed remotely by the user, and the system operates automatically dusk-dawn.
UPDATE (January 2020): I am happy to report that, after reaching out to the customer, the system has been in operation for over three years without any issues to date. They noted that it has survived some severe weather without so much as a hiccup, and it has even become a part of their seasonal holiday decor.

The finished lighting setup on the peace sign. The structure is about 4ft in diameter, and is exposed to direct sunlight year-round. Weatherproof LED light strip was used for the entirety of the sign, with triple-sealed solder connections on every hookup.
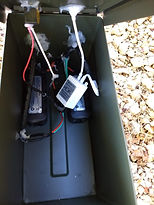

The control electronics as well as the batteries were placed inside a steel "ammo can" in order to provide safe and discrete storage for sensitive components (left). This container was buried in the decorative gravel landscaping just next to the peace sign.
The solar panel (right) is a simple 30w outdoor unit commonly used for RV battery charging. The panel sits behind decorative vegetation to conceal its location as best as possible. Direct burial cable was used for all connections, and is concealed under the decorative landscaping.

Connecting and modifying a truck bed topper
By far the most extensive installation of wiring I have attempted to date, this project required installing an entirely new wiring loom into a vehicle, as well as re-wiring the topper and connecting it to the vehicle wiring. The finishing touch was decorative LED lighting inside the topper itself.
At the start of the project, the customer simply requested that the truck bed topper have decorative lights, but upon further discussion, it was deemed that a full wiring setup of the topper was necessary. It was also requested that I enable the rear brake light on the topper since I would be installing new wiring anyway.
This was the most physically difficult project that I have undertaken to date, because the majority of the project involved mounting a new wiring harness underneath the vehicle. The total time spent on the project was only around six and a half hours, but nearly 5 hours were spent working underneath the vehicle.
Besides the initial changes to the project, there was only one major problem that arose, and it only became evident after the installation was complete. The main power fuses were specified improperly with the addition of the brake light wiring and failed during the first use of the lighting. Fortunately, I was able to replace the fuses with the correct models the next day at little cost to myself.
All in all, the customer was very pleased once the finished product was installed and working, and I was very satisfied with the successful completion of such a difficult project.
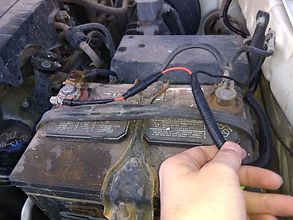
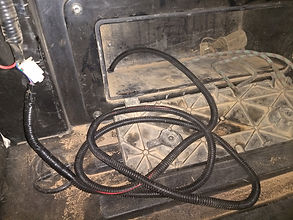

This project required installing a new wiring loom that ran the entire length of the truck. Installing this wiring proved extremely difficult, given that the majority of the wiring was run underneath the truck. When the wiring was complete, I had spent over 4 hours underneath the vehicle.
The finished wiring connects directly to the battery and is protected by multiple fuses.
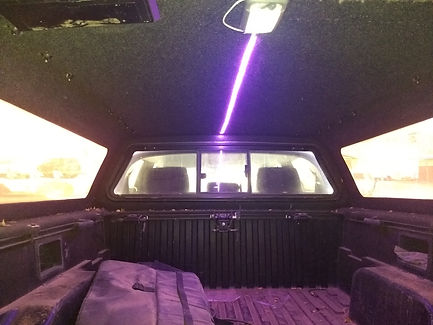
The finished lights add a rather interesting effect to the inside of the truck topper and should be bright enough to provide ample lighting in any situation.
The lights are controlled by a small remote, and can produce a variety of patterns and colors
Carpeting made it very easy to affix the lights to the inside of the topper with industrial velcro.